India’s Leading Casting Experts: Feinguss, Micro Fusion, Lost Foam & Lost Wax
Introduction
Hey there! Curious about how those super-precise metal parts for cars, planes, or medical devices are made? You’re in the right place! India’s casting industry is a global powerhouse, and today we’re diving into four awesome techniques: Feinguss Casting Manufacturers, Micro Fusion Casting Manufacturers, Lost Foam Casting Manufacturers, and Lost Wax Casting Manufacturers. These methods are the magic behind some of the toughest and most intricate components out there.
In this blog, we’ll break down each technique in a way that’s easy to get, share their benefits, and spotlight Meena Cast Pvt. Ltd., one of India’s top players delivering world-class casting solutions.
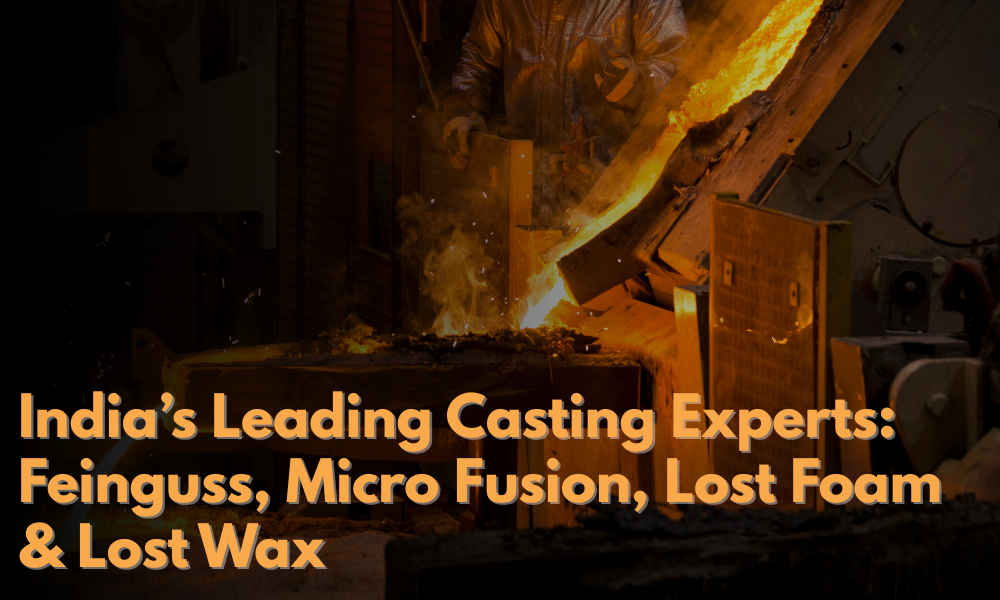
The Evolution of Casting in India
Casting in India goes way back think ancient sculptures to today’s high-tech parts. Over the years, India has built the skills, tech, and global reach to supply top-notch castings to Europe, North America, and Asia. Rajkot, Gujarat, is a major hub for this craft, and Meena Cast Pvt. Ltd. stands out for its innovation, quality, and ability to handle everything from small batches to massive production runs.
The Role of Sustainability in Modern Casting
It’s not just about precision anymore industries are going green, and casting is stepping up! Methods like Feinguss and Lost Wax are eco-friendly, cutting down on waste, reusing molds, and saving energy. Companies like Meena Cast Pvt. Ltd. are leading the way, helping industries lower their environmental impact while keeping quality sky-high.
Choosing the Right Casting Method for Your Project
Not sure which casting method is right for you? It depends on your project. Need tiny, super-detailed parts? Micro Fusion Casting Manufacturers are your best bet. Want big, complex components on a budget? Lost Foam Casting Manufacturers have you covered. For top-tier precision, Feinguss Casting Manufacturers or Lost Wax Casting Manufacturers are the go-to. The pros at Meena Cast Pvt. Ltd. make it simple by guiding you to the best method for your design, material, and budget.
What is Feinguss Casting?
“Feinguss” is German for “fine casting,” and it’s another name for investment casting. Here’s the deal: a wax model of the part is made, coated in a ceramic mold, then the wax is melted out, and molten metal is poured in to create the final piece. Simple but brilliant!
Benefits of Feinguss Casting Manufacturers:
- Super smooth surface finish
- Handles complex shapes like a champ
- Spot-on accuracy
- Less need for extra machining
- Works with tons of metals, like stainless steel and superalloys
Micro Fusion Casting: Small Parts, Big Precision
When you need tiny, intricate parts with crazy precision, Micro Fusion Casting Manufacturers are the way to go. It’s like Feinguss but focused on super-small components for industries like aerospace, medical, electronics, and instrumentation. Using detailed wax patterns and advanced ceramic molds, they nail those fine details.
Feinguss Casting Manufacturers in India, like Meena Cast Pvt. Ltd., are known for delivering export-quality parts that meet tough global standards.
Why Choose Micro Fusion Casting Manufacturers?
- Crazy precise dimensions
- Smooth surfaces with minimal finishing
- Perfect for tiny, detailed parts
- Cost-effective for small batches
Meena Cast Pvt. Ltd. is a top name among Micro Fusion Casting Manufacturers, offering custom solutions with fast turnaround and reliable quality.
Lost Foam Casting: Complex Shapes, No Cores Needed
Lost Foam Casting Manufacturers use a polystyrene foam pattern instead of wax. The foam is packed in sand, and when molten metal is poured in, the foam vaporizes, letting the metal take its place. No need for cores (those tricky bits for internal cavities), making it great for complex designs.
Dear Students, taking part in a Graphic Designing Course in Rajkot is an excellent idea if you want to develop a fulfilling career in design and unlock your imaginative side. trustworthy institutions and design institutes in Gujarat’s expanding city of Rajkot provide a range of skilled graphic design software applications.
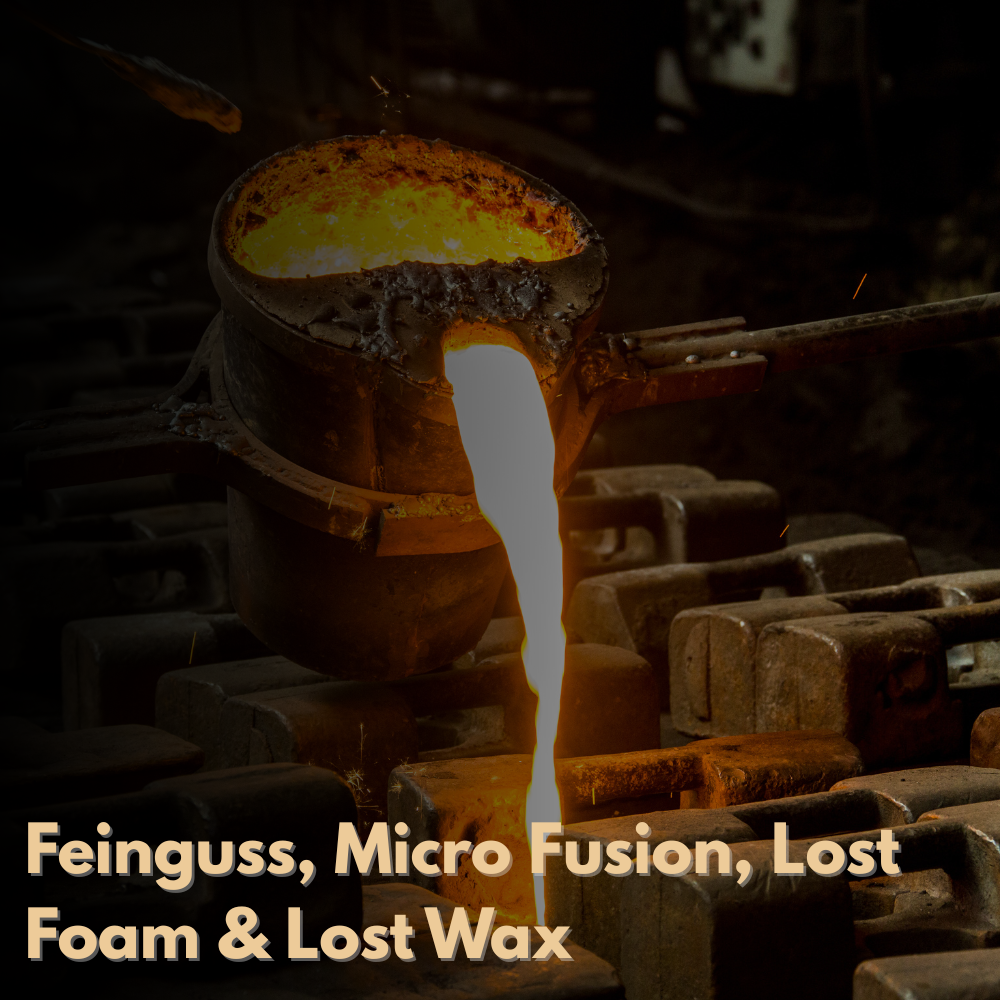
Advantages of Lost Foam Casting Manufacturers:
- Simplifies the process
- Awesome for complex or hollow parts
- Affordable tooling
- Consistent dimensions
- Fewer finishing steps
As leading Lost Foam Casting Manufacturers, Meena Cast Pvt. Ltd. exports high-quality parts to places like Germany, Russia, and Poland, keeping things precise and budget-friendly.
Lost Wax Casting: Ancient Method, Modern Perfection
Also called investment casting, Lost Wax Casting Manufacturers have been perfecting this technique for thousands of years. It’s like Feinguss: create a wax model, coat it in ceramic, melt out the wax, and pour in the metal. Today, it’s supercharged with automation, CNC machining, and high-tech systems.
Why Lost Wax Casting Manufacturers Are Still Popular:
- Incredible detail and finish
- Super accurate and reliable
- Works with high-strength, high-temperature alloys
- Great for both small and large production runs
Meena Cast Pvt. Ltd. uses cutting-edge tech and in-house labs to ensure every part meets strict global quality standards.
Why India’s Casting Industry is a Global Game Changer
India’s casting scene isn’t just about making parts it’s about delivering value, precision, and trust. Companies like Meena Cast Pvt. Ltd. are rewriting the game by combining cutting-edge tech with a customer-first mindset. Here’s why they’re a big deal:
Partnering with India’s casting experts means you’re not just getting parts you’re getting a competitive edge in a global market.
With decades of experience and a client base, Meena Cast Pvt. Ltd. is a casting superstar. It’s not just their facilities it’s their passion for quality, innovation, and keeping customers happy.
- In-house production with fully equipped testing labs
- Automated molding and machining for consistent results
- International certifications like TUV NORD DIN EN 9001:2015, PED, and IBR
- Exports to Europe, Russia, the USA, and the Middle East
- Rapid prototyping and custom solutions
Whether you need a handful of prototypes or a huge batch of industrial parts, Meena Cast Pvt. Ltd. delivers every time.
Industries Served by These Casting Techniques
India’s casting industry, led by experts like Meena Cast Pvt. Ltd., powers a ton of sectors:
- Automotive & Transportation
- Aerospace & Defense
- Medical Instruments & Implants
- Oil & Gas Equipment
- Energy & Power
- Textile Machinery
- Industrial Automation
Every part from Feinguss Casting Manufacturers, Micro Fusion Casting Manufacturers, Lost Foam Casting Manufacturers, or Lost Wax Casting Manufacturers keeps these industries running strong.
Conclusion
India’s no longer just a low-cost manufacturing spot it’s a hub of engineering brilliance. With growing demand for high-performance cast parts, India’s expertise in Feinguss Casting Manufacturers, Micro Fusion Casting Manufacturers, Lost Foam Casting Manufacturers, and Lost Wax Casting Manufacturers is more vital than ever.
Companies like Meena Cast Pvt. Ltd. show that quality, precision, and trust go hand in hand. Whether you’re a global OEM or a startup with a big idea, partnering with India’s casting pros means you get innovation, reliability, and world-class production.
Reach out to Meena Cast Pvt. Ltd. and see how India’s finest can craft your vision with precision and care.
About the Author
Article has been written by Khyati.